Why Choose Us
NDT Group offers a range of inspection and testing methods to detect defects and flaws in rail components without causing any damage to them. Our services enhance safety and minimize the risk of accidents and downtime due to defects or flaws in critical components.
There are several factors that influence rail defects and rail failures. These factors include bending and shear stresses, rail/wheel contact stresses, residual stresses, thermal stresses, and dynamic effects. Nondestructive testing (NDT) methods are used as a preventive measure against track failures and possible derailment.
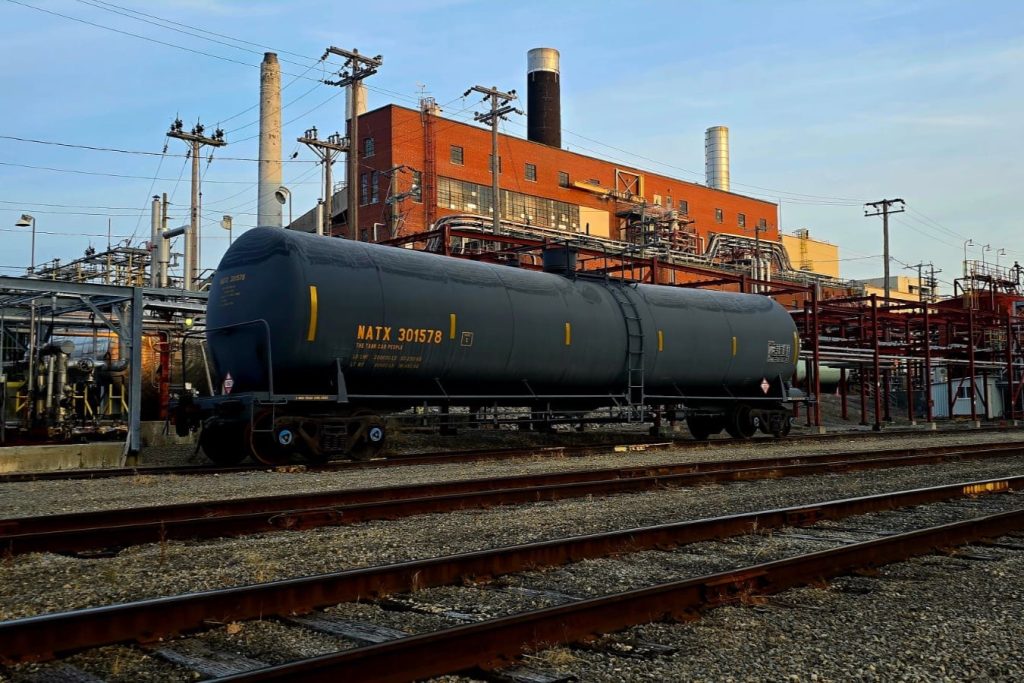
Our
Approach
service delivery process
The process typically begins with a comprehensive assessment of the specific needs and requirements of the rail industry client. The NDT Group works closely with the client to understand their goals, priorities, and the types of rail components or systems that need inspection.
NDT Group experts select the appropriate NDT methods based on the client’s requirements and the characteristics of the rail components to be tested. Common NDT methods used in the rail industry include ultrasonic testing (UT), magnetic particle testing (MT), dye penetrant testing (PT), radiographic testing (RT), and eddy current testing (ET).
The NDT Group employs highly trained and certified NDT technicians who are experienced in performing inspections on rail components. These technicians are certified according to industry standards and regulations.
NDT Group invests in state-of-the-art NDT equipment and technology that is specifically designed for rail industry applications. This includes specialized sensors, probes, and scanners tailored for testing rail tracks, wheels, axles, welds, and other critical components.
Preparation: Prior to inspection, the rail components are prepared, cleaned, and prepped as needed to ensure accurate and reliable testing results.
Testing: Technicians perform the selected NDT methods, such as UT for detecting internal defects or MT for surface crack detection. Depending on the method, inspections can be conducted while the rail components are in-service or during scheduled maintenance and overhaul.
NDT Group analyzes the data collected during the inspections. Advanced software tools are often used to process and interpret the results. A detailed report is generated, documenting the findings, including the location and size of any defects or anomalies detected.
Based on the inspection results, NDT Group provides recommendations to the rail industry client. These recommendations may include maintenance actions, repair procedures, or component replacement to ensure safety and reliability.
NDT Group ensures that its services comply with industry standards and regulations, such as those set by organizations like the American Society for Testing and Materials (ASTM). Quality control and assurance procedures are in place to maintain the highest standards of accuracy and reliability.
In addition to periodic inspections, NDT Group may offer continuous monitoring solutions using technologies like remote sensing or automated inspection systems to provide real-time data on the condition of rail infrastructure.
NDT Group may also provide training and education services to the rail industry, helping clients understand NDT methods and the importance of safety and reliability in rail operations.