Conventional NDT
Seeing Beyond the Surface
Conventional NDT Services
Conventional non-destructive testing (NDT) techniques provide a non-invasive means of inspecting and assessing the integrity and quality of materials, components, and structures.
Some of the key parameters and flaws that can be measured using conventional NDT techniques include:
- Dimensional Measurements
- Surface Defects
- Weld Integrity and Quality
- Material Composition and Properties
- Thickness and Wall Loss
One crucial advantage of conventional NDT is its versatility, as it can be applied to a wide range of materials, including metals, plastics, composites, and more. This flexibility allows for comprehensive inspections across diverse industries such as aerospace, manufacturing, automotive, energy, and infrastructure.
NDT Group offers a variety of methods that are chosen depending on the type of material, the nature of the inspection, and the desired parameters to be assessed.
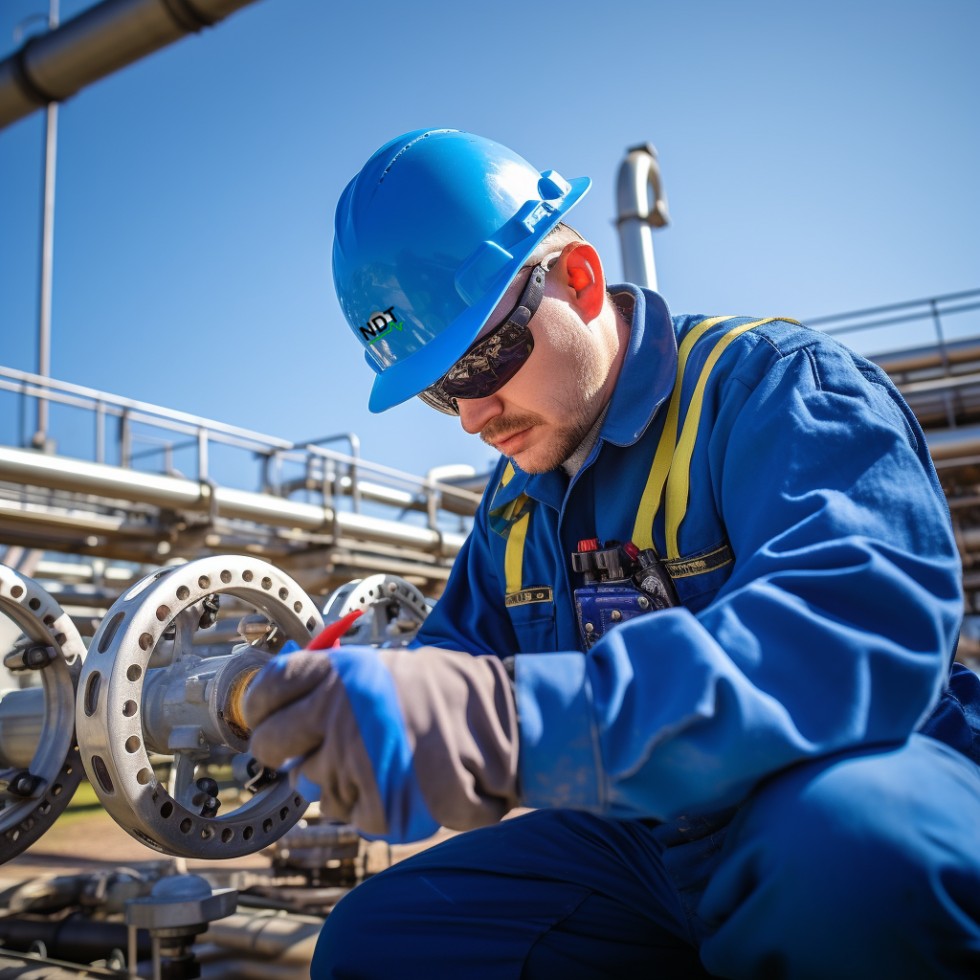
Techniques
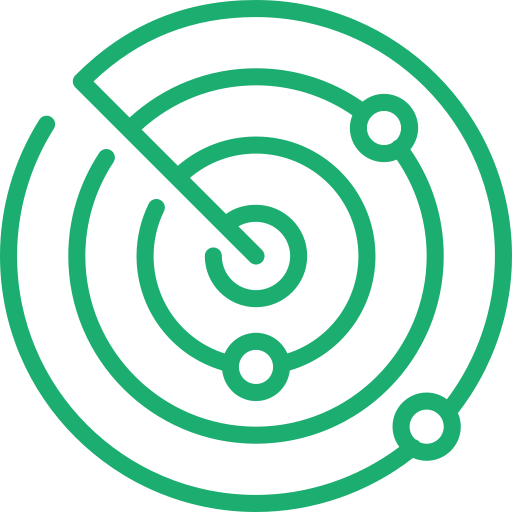
Ground Penetrating Radar (GPR)
Uses electromagnetic waves to detect and map subsurface features, such as objects, voids, or changes in material composition.
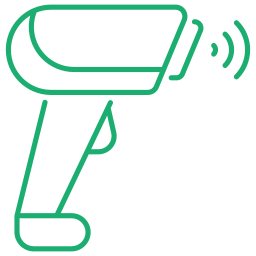
Laser Induced Breakdown Spectroscopy (LIBS)
Analyzes the elemental composition of a material providing information about its chemical makeup including Carbon.

Liquid Penetrant Testing (PT)
Application of liquid dye to the surface of a material, allowing it to seep into surface defects, and then applying a developer to make the defects visible for detection and evaluation.

Magnetic Particle Testing (MT)
Utilizes magnetic fields to identify surface and near-surface defects in ferromagnetic materials by detecting variations in magnetic flux.
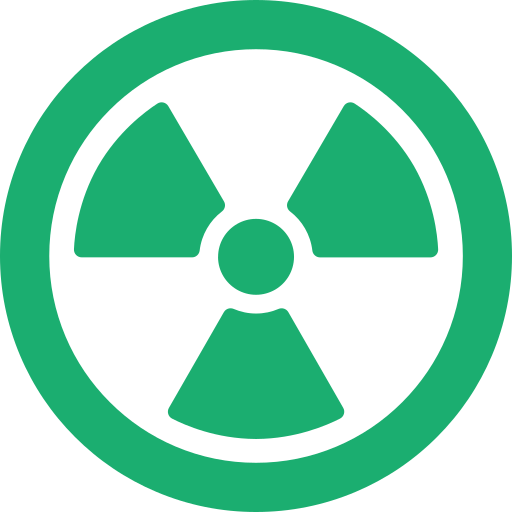
Radiographic Testing (RT)
Uses X-rays or gamma rays to capture images of the internal structures of materials, allowing for the detection of defects and evaluation of their characteristics.

Ultrasonic Testing (UT)
Uses high-frequency sound waves to detect and analyze internal flaws measure material thickness, and assess the integrity of structures or components
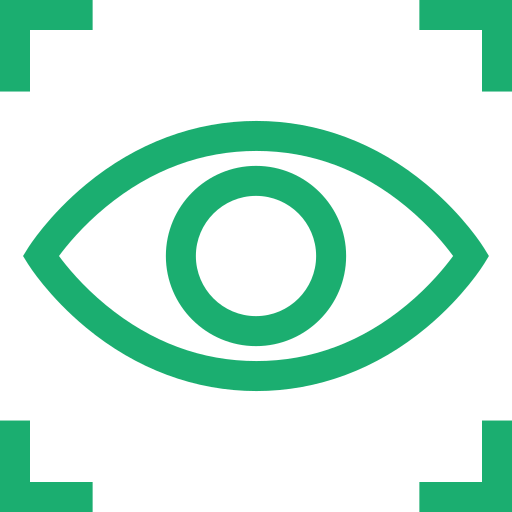
Visual Inspection
Direct observation of the surface and accessible areas of a component or structure to detect any visible defects or anomalies.

X-Ray Fluorescence Spectroscopy (XRF)
Determines the elemental composition of a material, typically metals and alloys, to verify its grade, composition, and ensure it meets specified requirements.